How linear guide rails make precision machining possible
CNC technology has come a long way over the last few decades, with constant industry advancements shifting the way work is done and expanding the scope of what is possible in the shop.
Among these advancements is the development of linear guide rails (also known as precision contour guide rails), which opened a whole new door to the world of high-speed machining.
Here is a look at the evolution of guide rails and how the precision contour guide rail system helps CNC operators achieve a more precise and efficient process on every project.
The evolution of guide rails
Axis motion is an essential concept of machine tool design, wherein the machine moves along the x, y, or z-axis as defined by the guide rail system.
Early on, guide rails were fairly simple and had a v-guide and a roller that only moved back and forth. This concept was later developed into round bars, which worked well but were unable to handle heavy loads or to perform heavy machining which is particularly relevant in the metalworking industry where the weight of certain components for machine frames and more resulted in the use of ground square rails. These also worked well for a while.
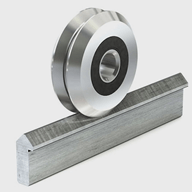
V-Guide and Roller
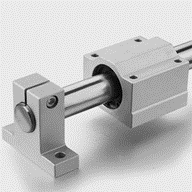
Round Bars
Then high-speed machining arrived, and none of these previous technologies were able to get the job done effectively. The industry had reached its speed limitations in terms of acceleration and deceleration (acc and dec).
Then a couple things happened.
Manufacturers began using structural steel for machine design, which was very predictable in its characteristics and thus helped open the door for computer design as a means of engineering different components.
Because of this, manufacturers also had to create a compatible guide rail system that would maintain rigidity while allowing rapid acc and dec.
The solution was precision contour guide rails.
Precision contour guide rails
The precision contour guide rail system is really based on two components the rail and the bearing track but no component is more critical than the ball bearing. Within the system, recirculating ball bearings connect the rail and the bearing truck, similar to how ball screw technology works. This is what drives the increased precision of these machines while minimizing play and backlash during operation.
Because contact between the rail and bearing track is fairly limited, the machine can acc and dec rapidly and achieve increased productivity on small- and large-scale projects. Linear guide rails allow everything to be predictable so users can incorporate engineering software to help in the design process.
ShopSabre’s use of precision contour guide rails
ShopSabre’s machines utilize 25mm linear guide rails with triple-wiper linear guide bearing blocks. The use of two bearing blocks on each rail ensure the cut forces are equally distributed over the rail to reduce the amount of wear and noise.
The triple-sealed bearing blocks help ensure that debris and dust buildup on the rails do not lead to pre-mature failure, while its still important to perform normal housekeeping. The wipers extend the bearing life and performance. The design also effectively makes the machine a self-cleaning system, reducing the need to wipe down rails or watch for buildup both during and after operation.
Our machines built with large linear guide rails and bearings help reduce maintenance and wear compared to smaller bearing systems.
Experience CNC the way it was meant to be with ShopSabre
ShopSabre manufactures world-leading CNC routers and CNC plasmas to provide hobbyists and shop owners alike with unmatched precision, efficiency, and versatility. Whatever your goals may be, we are dedicated to helping you produce outstanding results at a fraction of the labor and cost.
Our Industrial Series (IS) and PRO Series CNC routers provide industrial capability for a fraction of the price, while our SideKick CNC plasmas deliver professional quality at an entry-level cost.
Shop our unmatched collection of CNC routers and CNC plasmas today to experience CNC the way it was meant to be.